HDPE (High Density Polyethylene) Explosions – Korea ( Yeosu Industrial Complex )
On 14 March, 2013, an explosion occurred in the HDPE silo at Yeosu Industrial Complex, killing six workers during a manhole installation and injuring eleven workers. In addition to human loss, it caused property damage to nearby factories and destroyed three silos at the factory. The accident investigation revealed that HDPE powder was attached to the inner wall of the silo body, which was filled with air, and the bag filter. During the manhole installation work, some powder dust fell off the lower side and created a deposit due to the vibration caused by tools. The primary explosion happened when the flammable material inside the silo was ignited by the welding sparks during the manhole installation. Heat and shock waves generated in the first silo, as shown in Figure 2, and spread to neighboring silos through the piping connected to the outlet of the HDPE powder bag filter, resulting in the secondary explosion.
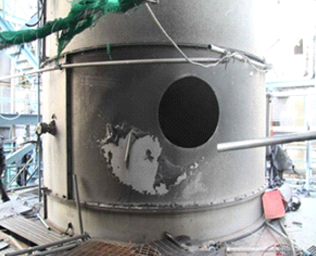
The silo where the dust explosion ffirst began
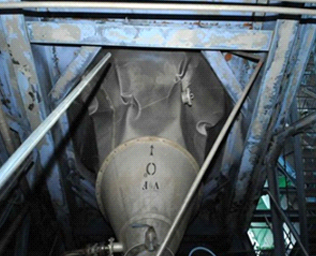
Image off silo bottom due to sudden impact
Details of the accident are as follows: Welding was carried out at six different positions in the silo where the fire was ignited. In general, welding is known to be a very powerful ignition source that ignites all types of explosive mixtures. Aluminum alloy, which the silo was made of, has a thermal conductivity three to five times higher than that of iron alloy. Polyethylene dust attached to the inside of the silo and the bag filter acted as a combustible material and was ignited by welding sparks, resulting in fire. Generally, combustible dust can cause an explosion if the particle size is less than 420 µm. At this time, the polyethylene dust collected inside the silo had an average size of about 60 µm, which is a condition that easily causes an explosion. It is assumed that an explosive environment had been created because of the accumulation of dust and flammable gas. To summarize the progress of the explosion in the silo: (i) The occurrence of fire during welding, (ii) the diffusion on the wall, and (iii) an explosion in the upper position. During the work after the initial gas measurement, continuous ventilation and measurement of gas must be carried out. Unfortunately, the organization’s permission to work without ensuring that no explosive mixtures were present in the silo caused the dust explosion.
IMPERIAL SUGAR
The explosion at the Imperial Sugar refinery in Port Wentworth, Georgia
in February 2008 provides a lesson in the importance of understanding
the hazard created when combustible dust is released outside of the
process equipment and into a building or structure. A complete report
and a video describing the event are available from the Chemical Safety
Board (CSB 2009).
The explosion likely started in a belt conveyor located underneath the silos. The conveyor had been recently modified to add a sheet metal enclosure to improve product quality. The enclosure allowed the accumulation of a concentrated dust cloud in the interior. The ignition source might have been an overheated bearing or belt support. The pressure wave from the initial explosion spread throughout the building, buckling the floors and dislodging dust that had accumulated in the building. The dislodged dust ignited and created fireballs resulting in several secondary explosions throughout the building. The CSB report notes that secondary explosions occurred on all four floors. Fourteen people were killed.
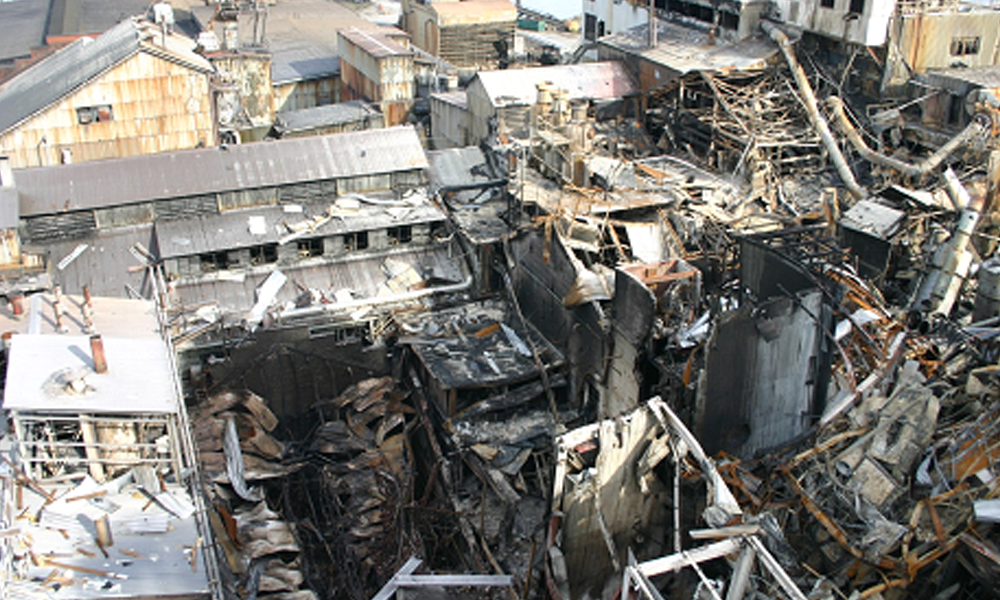
The refinery consisted of three large (374 m3, 13,200 ft3) silos, severaltypes of conveyors (e.g., belt conveyors, screw conveyors, and bucket elevators), mills, and packaging equipment. The refinery was housed inside a four-story building, with the silos extending from the ground to above the top floor. The CSB report states that the sugar handling equipment was not adequately sealed, resulting in large quantities of sugar being spilled onto the floors. An internal inspection noted that “tons of spilled sugar had to be routinely removed from the floors and returned to the refinery for reprocessing”, providing an illustration of the amount of material regularly spilled.